ATC Channel 7
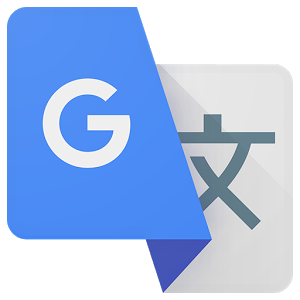
Introduction
The ATC building, originally called Television Production Center Buenos Aires, was built as part of the work carried out on the occasion of World Cup 1978, held in Argentina.
This Center was generated images in black and white and color football games transmitted to Europe, America, Africa, Asia and Oceania.
After the championship, the complex was awarded to Channel 7, which changed its image under the name of Argentina Televisora Color (ATC). Channel 7 is the only public channel in the orbit of the state and national coverage.
Location
Set in a green area north of the city of Buenos Aires. In the same area are other important buildings such as the School of Law, the MALBA, the Centro Cultural Recoleta and the Recoleta Cemetery. ATC Waterfront property can see the sculpture Floralis Generic.
The land is bounded by Austria and Tagle streets, Avenida Figueroa Alcorta and Bartolomé Miter railroad tracks, and its area of nearly 3 hectares.
Concept
Program requirements demanded a response architectural floor occupying an area of almost 3 hectares, the functions required to solve three types of heights: Office and 3-meter room, studios for 12 to 15 meters and workshops with approximately 9 meters.
The party was taken because of the very short time available for the design and construction. This resolution allows for maximum flexibility to meet all required functions and the maximum simplification of work tasks.
The building works under a semi-public space. The park extends over the building, continuing the green spaces surrounding the farm.
A functional scheme very tidy drawer is covered with a triangular section that solves the continuity of the park and the problem of “taking” the scale of the residential neighborhood bordering the campus. Emerge from this crate four equal blocks containing the studies and give you a more abstract architectural quality. From the point of view of the composition is two buildings: one outside and one inside without outside without interior. One private and one public that are tangent, which have a common boundary.
The internal space is clearly zoned into three parallel bands of use.
Spaces
The premises were organized in three parallel strips arranged perpendicular to Avenida Figueroa Alcorta. The first, lying on the street Tagle for the workshops, the second for the studies, the third for offices, dining, etc.. One roof, with a constant slope that descends from Eagle Street to the height necessary for workshops, offices and covers reaches the level of ± 0.00 m square. From this roof closed emerge four volumes that correspond to the studies. He recovered well, the roof to the park uses, generates about the same a dry place, preserving a green area of great value both for its size as the old copies that integrate.
The four main volumes are surrounded by a perimeter skylight to allow natural light into the heart of the plant. The last local band to visually integrate with the square and lining an artificial lake with an island that is the transmission tower.
The three functional bands, workshops, studios and offices where the plant is organized, are separated by the two main channels of movement, perpendicular to Avenida Figueroa Alcorta and leaving the band in the center that contains the studies, the circulatory pattern is complemented with cross streets.
The axis linking service circulatory sealing areas states: warehouses, workshops, machine shops and, of course, studies. The main circulation axis leaves aside the volumes of studies and other public-administrative area, more flexible in its uses and expression. In both runs the varied use of materials and colors avoids a monotone image without losing its “industrial manufacturing or” inside the building.
A cross travel, perpendicular to the former, unveiling the successive and gradual passage of the fully enclosed areas open, expressive elements of this gradual interpenetration: perimeter skylights that, exploiting the volumes of studies, engage in general cover ; rupture plane drilling deck reserving places for existing trees, use of translucent materials that privatize use areas without losing continuity of the office sector, organization of the receipt around a square courtyard inside. These resources provide adequate natural light and interesting relations to the outside, avoiding claustrophobic feelings and admit that the user of the square life glimpse of the complex. The tour ends in the confectionery cross dining through its curved ceiling, carpentry inclined and achieves the necessary foreign expansion and fluid connection with the plaza space.
Access for actors and directors is on Figueroa Alcorta Avenue, thence some technical movements, access to services are in a side street tangent to Tagle, the only public access to a studio specially equipped for it, its access is occurs through an open hall on the surface of the square. The band hosts service support functions to record activities such as outdoor equipment, depots and warehouses, maintenance shops electronic and electromechanical, makeup rooms, hairdressers and so on. Both areas make contact in the central belt, where the studios are located.
The most important activities of the strip technique is the electronic control central, located at the geometric center of it, which combines the information they transmit partial controls, and from which signals are broadcast through the tower. This plant and other electronic services are possible in view of visitors through a window inclined. On the side streets technician installed a mezzanine floor where are located the various channels and equipment. In the last band and around an open courtyard located in the plaza waiting areas and general management area that has parking and separate entrances on the avenue.
Around the perimeter of the building the canteen is the only region with foreign expansion and exit to the island in this sector have been opened craters octagonal square in the ceiling, keeping as many trees and providing natural light through a carpentry inclined.
Studies were divided into two rooms of audio 9.25 x 14.60 meters and one for big shows, with public acceptance of 38 x 23.70 meters.
In all cases they are formed as independent units from the functional standpoint, static, noise and heat. Each unit is flanked by partial production controls, sound and lighting, neighbors to the technical area and changing rooms and locker rooms tied at service.
In drawing the picture of the sloping garden, are superimposed: the floor of the old classic of the original park design, repetition of the module square of the inner frame and a set of elements that frame a view and collect from major urban routes are made up significantly more important. There is also in the public colonnade leading to the entrance of larger study, an allegory monumental tribute to the men’s national spectacle. The four volumes of concrete in the light of studies emerging from dry place off the floor and reach 20 meters in height.
The artificial lake, the storm drain with a central island which is an outward expansion of the dining room, spoke in a stream running through the plaza lengthwise. The transmission tower emerges from the water surface and reaches 55 meters high.
Facilities
The facilities of a building over in a single plant that integrates variety of uses required a careful study of the thermal conditions to achieve an appropriate solution.
In the recording studio with high temperatures, caused by light fixtures should be noted that an event changes may occur in air quality acoustics.
Therefore been established, a central fluid conditioning (located on the fringe of services), with equipment installed in the full technical support for the different zones.
Thus was solved the problem of conditioning areas with diverse requirements ranging from newsroom news with uninterrupted operation temperature of 24 ° C until the film processing room, with strict fixed conditions of humidity and constant temperature of 23 degrees C (independent of changes in internal loads) and up studies, with peak performance, with 50% RH and a temperature of 24 º C (with variations of ± 2 º).
All equipment was installed part on a technical level except the central control area, which are located at ± 0.00 m in this area since the handling of the equipment is part of normal operations.
The strict acoustic conditions forced the studies necessary to minimize the output speed of the air, not exceeding 2.5m / s. The movement speed is 5m / s in Study 1, 4m / s in studies of 2 to 5 and 3 m / s in audio. This, in turn, increased the already huge section of the conduit. For this reason it was placed on the studies: hanging outside the slab in Study 1 and supported in the same in the other.
Various anti-vibration isolations avoid any transfer by transmission, while avoiding traps sound absorption of noise from outside.
Static independence of each study is the prerequisite for adequate acoustic insulation. This acoustic insulation, each consisting of a small enclosure (walls, floor and roof) reinforced concrete 25 cm thick resting on neoprene dice 20×20 cm. A “cap” (wall and roof) also reinforced concrete 30 cm thick separated 45 cm from the internal structure, complete insulation from external sources. Covering walls and ceilings are made with glass wool panels with armed resonators on an autonomous structure which in turn are superimposed cycloramas.
The lighting is made from metal grates hanging from the concrete slab, fixed and distributed in parallel bands in studies 2 to 7, and folding cloth over the entire surface in study 1. The floor boards is not supported and must meet important conditions of hardness, is resolved as self-leveling epoxy based on monolithic.
The thermal conditioning equipment are autonomous from the system, ranking hanging outside the slab in the case of Study 1 and supported in studies 2 to 7, since for cover under their respective flags lamps had a lower height of beams allowing thus unifying the four volumes. The connections to the room racks are resolved through a floating floor system covering the entire surface of the areas of controls and move tangential to the study. It consists of sheet metal stampings, plastic laminate coated on high strength of about 0.60 x 0.60 meters, supported on regular media.
Structure
The structural solution and constructive complied two fundamental constraints: the short time to the project and the special acoustic conditions in certain areas. This led to employ a special structural system for studies and a frame of columns and beams whose simplicity demanded equal short run time and provide great flexibility in plant, given the variation of functions in the program requested. The plant is modulated at 7.20 x 7.20 square meters. For the concrete structure used a mixed system of planed wood planking, metal and reinforced plastic. At 1400 cm columns of 40×40 individual foundations were made.
In the beams of 0.40 x 0.90 meters drilling section provides addresses for both air conditioning ducts.
Materials
Foundations: Pile belt pre drilled from studios to Tagle, and isolated base of reinforced concrete beams bracing the rest of the work.
Structure, columns and beams of reinforced concrete double walls and concrete ceiling of 25 cm and 30 cm with a separation of 45 cm made with metal casing and reinforced plastic; termination: concrete studies in sight.
Roofing: concrete slabs. Insulation: Neoprene-hypalon studies and mezzanines, asphalt, glass wool, aluminum foil and roofing asphalt applied at 16 layers.
Exterior walls: reinforced concrete walls 12 cm, pre-molded plates lined with green granite Alpe wash.
Interior walls: glass divisions, concrete blocks filled with vermiculite, marble, glass blocks, marble from Carrara.
Plasters and linings: brick walls, racotón relief; in circulation, aluminum slats black; studies, galvanized iron perforated trays, in studio work, surface scrim panels.
Carpentry: aluminum exterior tempered glass, interior iron, stainless steel and wood.
Ceilings: plaster, concrete, visible, aluminum slats, soundproofed, mirror.
Interior flooring: granite tile 40×40 cm, carpeting, belts made of Carrara marble; entablonado color to change, floating floors clad in stainless steel and plastics into high strength, self-leveling epoximonolítico. Stairs and circulation: profiles and painted metal grill, reinforced concrete termination girl saw red granite, marble gray concrete Punilla termination.
Solados External baldosones Alpe green granite 50×50 cm strips of labradorite granite mountains fiamatado girl.
The play went back and forth 24,773 meters cubic of concrete.
The transmission tower reaches 55 meters high and consists of a reinforced concrete structure of high inertia (three equal circles inscribed in a circle 6 meters in diameter) due to the need to minimize the oscillation peak in the which also houses a water tank. It was built with sliding molds at a speed of 20 cm / h.
We used over 180 tons of metal in the manufacture of ventilation ducts and 10,500 meters of pipes to distribute hot and cold water.