De Brug – Unilever Best Foods European HQ
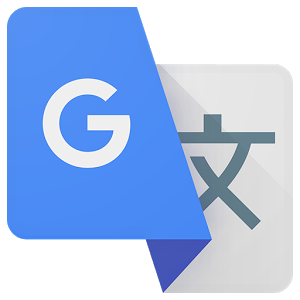
Introduction
The Unilever Blue Band factory in Nassaukade, is over 120 years old and is currently the largest margarine factory in the world, with a production of more than 200,000t of margarine and 10,000tn of peanut butter. After this time the company considered that it was time to undertake a remodeling of the facilities and provide it with new offices for its headquarters.
The De Brug Bestfoods Unilever offices building in Rotterdam is known for its spectacular architecture that led to the use of airspace with the consequent release of the ground level. But what makes this 7,500-ton building unique is the story of how it reached its extraordinary location.
“Brug” means bridge in Dutch and it was the use of bridge construction techniques that helped the team carry out its bold design. The steel superstructure was built elsewhere as a temporary structure, moved with huge trailers and then slid down a track to its position on the roof of the Unilever factory.
A new building could have been built in a large empty space next to the Unilever factory and that was the company’s first intention, but JHK Architects‘ avant-garde proposal made more financial sense since that space could be used to build lucrative homes . As soon as JHK came up with the bridge concept, the contractor Dura Vermeer contacted the manufacturer of bridge steel Hollandia to find out if the design could be built. Hollandia had experience in addressing difficult structures, one of his most challenging projects was the technically complex London Eye. Once the engineers analyzed the project from every possible angle, the team stated that De Brug could be built quickly, safely and at a reasonable cost. What’s more, the entire operation would only require the factory to close for one day, ensuring the continuous manufacture of Unilever Bestfoods products.
Location
De Brug is located on the south bank of the Maas River in Rotterdam, Holland, near the old Hef railway bridge, in Nassaukade 5. From the Rotterdam Central Station you can reach Nassaukade by bus 48.
Concept
The building is inspired by the nearby drawbridge and lives up to its name De Brug, being built as such on a historic factory already existing since 1891, creating an interesting architectural contrast. This four-story office block extends over a factory complex on the banks of the Maas River and resembles a giant trestle table with architectural models stacked beneath. The building that was designed by architect Chris de Jonge, is the headquarters of the multinational Unilever.
The design of the De Brug building is a very efficient way to use the limited space of the existing factory. During construction, the operations of the plant continued 24 hours a day and the existing plant remained intact. This was made possible by the construction of a temporary structure at a nearby site and the transfer with electric elevators to their final destination when the construction was completed.
Spaces
De Brug (The Bridge in Dutch) consists of a four-story office building with 3.60m high each and an area that covers approximately 133×32 meters. The lower part of these four floors is 25 meters above ground level, directly above the existing industrial complex. The main entrance is on the pier, next to the classic 19th-century office building. The elevator and the stairs are in the inner courtyard, opening the floors. In this “bridge” increasingly large gaps have been incorporated to bring daylight into the building, but also to ensure visual contact between the pier and the lobby on the ground floor or the upper spaces. The depth of the floors allows them to be divided into three zones of 10.80m, two lateral zones that run along the longitudinal walls and another central zone.
On the ground floor, under the parking deck, there are specific functions for the user, such as a commercial space, a storage room with annexes, toilets and a reception.
On Nassaukade Street is the entrance to a passage with a glass roof that leads to the large and tall lobby, where the reception, stairs and elevator are located. This passage provides the connection between the street and the central elevator shaft, which then opens to the office located above the factory.
The place occupied by the former Blue Band factory building has been used to create a parking lot with capacity for 471 employees’ cars. The truck path to the underlying factory site is in Nassauplein.
Structure and materials
The main materials used in its construction were steel and glass, combined with reinforced concrete bases in the floors.
The building is constructed as a steel structure combined with a concrete floor with steel plate. Because the building rests on only three supports, the facades require large steel lattices. The ensemble gives the building an appearance of an ancient bridge to which the building owes its name, De Brug in Dutch, The Bridge in English. To minimize the proportions of the steel structures, lightweight concrete has been chosen instead of the one with a gravel base and thereby lighten the pressure on the floor. A low vibration and ground displacement pile drive system has been used to lay the foundations of the building.
The central axis lined with a metal panels facade is located on the existing building and provides the great intermediate support for the bridge office. This central axis also includes the elevator section, the flight ladder and the technical rooms required for the operation of the building
Building
During its construction the production in the existing factory did not stop, since the components of the new construction were carried out in a totally industrial way and transported through the Maas river to the place, where they were later connected in height.
The temporary steel superstructure was built in a nearby area and once on the site by a special track and elevators it was slid to its position on the roof of the Unilever factory, 25m above the pier, the same height that it would definitely have , and on that structure De Brug was built. Once the temporary structure was finished, the central beams and the rest of the frame began to be placed. To avoid developing an unwanted force in the steel construction, jacks were used to ensure that the suspension points in the structure were at the correct level.
To keep the weight to a minimum during transport, the concrete floors were poured once De Brug reached its final position. The glass and the rest of the interiors were also installed on site.
The facade elements are mounted from the inside. The project is, therefore, a unique example of space intensification in built locations.
Air conditioning
From the moment of its projection the parties agreed that one of the key factors would be sustainability in a broad sense, including heating and cooling. With an area of almost 16,000m2, four levels, the abundant use of steel and almost fully glazed facades, although double-paneled, was an important challenge.
Low temperature heating radiators were placed to counteract the downflow of cold air. These radiators, as well as the roof cooling system, use river water as a source, being heated by a heat pump.