Marina Bay Sands
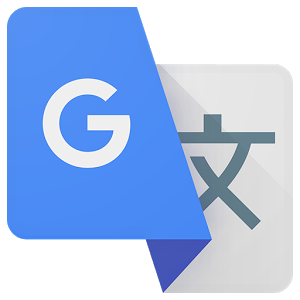
Introduction
Marina Bay Sands is a complex of high density, mixed use, the construction reached $ 5.7 billion.
Designed by architect Moshe Safdie for Las Vegas Sands Corporation, its facilities offering a surface of 845.000m2 stand on the boardwalk of Singapore, creating a gateway to the city and providing a dynamic environment for vibrant public life site. Safdie was invited to join Las Vegas Sands Corporation for the development of a competitive project design and present it to the Government of Singapore. The project has been awarded CTBUH 2010 Best Tall Building Awards, Finalist Asia and Australasia Region.
Situation
The Marina Bay Sands complex has been built on the waterfront Financial District of Singapore ,新加坡共和国(in Chinese), 10 Bayfront Avenue.
Concept
In the words of the architect: “… Marina Bay Sands is really more than a construction project, is a microcosm of a city rooted in the culture of Sigapur, its climate and contemporary life. Our challenge was to create a public place vital urban district scale, ie facing a mega-scale project and invent a cityscape that works on a human scale… “
Urban Structure
Safdie designed an urban structure that weaves together the components of a complex program with a dynamic urban crossing roads and public meeting place.
Inspired by the great ancient cities that are arranged around a major thoroughfare, Marina Bay Sands is organized around two main themes running through the neighborhood and give a sense of direction, placing greater emphasis on the pedestrian street, as the center of civic life.
Spaces
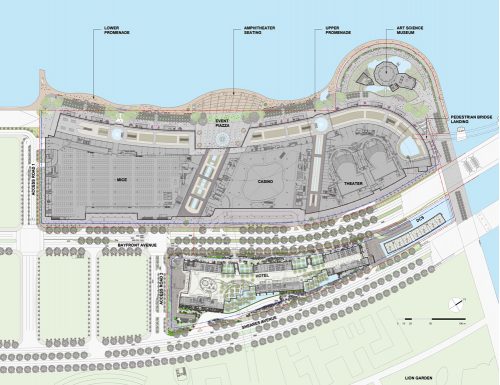
Its facilities offer a hotel with 2,560 rooms, a convention center, shops, restaurants, theaters, museums and a casino.
This new urban space integrates the waterfront boardwalk, some 74,000 square meters of small arches at various levels and the iconic ArtScience Museum on the promontory. Located along the network of public roads there are also two theaters with 4,000 seats between them, a casino, a convention center and exhibition of 9,000m2 and 5,000m2 a public square with a striking hydraulic adjustment, according to events.
Combining internal and external spaces and providing a platform for a wide range of activities, this vibrant “cardo maximus” of the century, or large gallery, also connected with the metro and other means of transport.
Torres
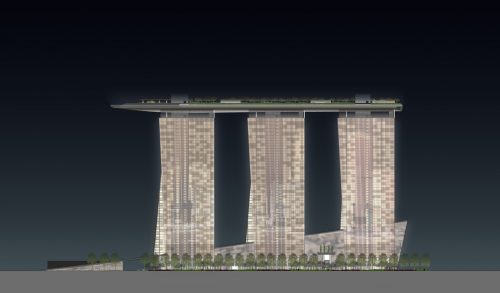
The three hotel towers 55 floors fastened to the floor and connected at the top with an air park of 1 hectare. An engineering marvel almost 200 meters above sea level, the SkyPark tower to tower extends 65 meters and flies in one end. Sleeps a public observatory, gardens, a pool of 151 meters long, restaurants and jogging trails, and offers far reaching views, a formidable resource in a dense city like Singapore.
- SkyPark
Protected from the winds and with 250 trees and 650 plants, SkyPark celebrates the concept of the garden city, which has been the foundation of the strategy of urban design in Singapore. Length is 340 meters from the north end to the south end end with a maximum width of 40 meters.
With its 65 freestyle creates one of the largest public cantilevered world. The pool of 1.396m2 is the largest outdoor swimming pool and by that time made, has 145 meters trailing edge. The whole park can accommodate up to 3,900 people
Grounds
A series of garden terraces provide ample green space throughout the complex, extending the tropical scenery from the Marina City Park to the Bayfront.
The landscape network reinforces urban connections with the environment, being accessible to the public all levels of green spaces and tropical plantations, through the broad pedestrian streets overlooking the sea. Half of the roof of the hotel, convention center, shopping center and casino complex are covered with trees and gardens.
Moshe Safdie selected five international artists to create eight monumental public art installations at Marina Bay Sands, James Carpenter, Antony Gormley, Ned Kahn, Sol LeWitt and Chongbin Zheng. The artists worked closely with Safdie to ensure that site-specific commissions dynamize complement the architecture and public spaces.
Construction
Program
- Hotel: 2560 luxurious rooms in three towers, with a total of 265.683m2
- Sands SkyPark: the three hotel towers are connected at the top, at 195 meters high by a park of 9.941m2 which houses a public observatory, jogging trails, gardens, restaurants, lounges and an infinity pool. This tropical oasis of 1.2 hectares is longer than the height of the Eiffel Tower and large enough for four jumbos to park A380s.
- Casino: The casino “atrium” has four levels of play and entertainment in a total space of 15,000 square meters. Atrium ceiling hangs a lamp 7 tons with 132,000 Swarovski crystals and 66,000 LEDs.
- Shop over 74.322m2 of retail space and restaurants.
- Sands Expo and Convention Center: 121,000 m2 of flexible convention and exhibition space, including one of the largest ballrooms in Asia with an area of 8,000 m2 and a capacity for 11,000 people.
- ArtScience Museum: 15,000 m2, of which 6,000 m2 corresponds to a gallery, 3,000 pond lilies with a palm tree 80 meters, 62 meters in diameter on level and 11 deep.
- Theatres: 21,980 square meters with a total combined capacity of 4,000 seats
- Crystal Pavilions: 5,914 square feet housing shops and nightclubs, the first steel and glass structure built in Marina Bay.
- Plaza event: 5,000 square meters with capacity for 10,000 people in events of local and international.
Structure and materials
The general form of the Hotel Marina Bay Sands was driven by the architectural requirement of continuous atrium throughout the three towers. The geometric flare resulting structurally resolved by prestressed concrete slabs and trusses cutting on several floors, located between the opposite halves of construction and through engine rooms average. The asymmetry of the buildings demanded detailed construction sequence analysis to assess the continuing deviation of the towers during erection. Moreover, the only way to each tower led to differential movements imposed by the load, which further complicated the engineering design SkyPark rooftop and support. Each of these challenges were addressed and resolved through close collaboration between design, construction and customer.
Towers Hotel
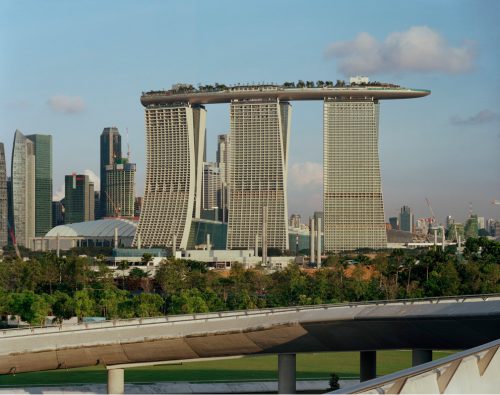
The building of the hotel towers with 55 floors was a critical time and design the first challenge for the engineering team. The flared base towers to create the conical atrium lobby is continuous and runs along the three buildings. The taper of the base created a significant technical challenge because of the asymmetric shape and curves in the legs that allow each tower is supported on the opposite side vertical legs. As a result, primary lateral forces imposed on the building applicants are governed by the effects of gravity rather than wind or seismic effects.
Structural flare
Walls reinforced concrete thickness ranging from 28 inches at its base to 20 levels higher plants are found in the centers of 10 meters, within each of the three towers. Shear walls serve as vertical and transverse primary structural system of the three buildings.
Additional cores also created with concrete walls are located in both legs of each building containing the hotel longitudinally and helping to prevent the exit plane buckling shear walls within relatively narrow legs of the towers.
The requirement for such a restriction in the design after rigorous analysis of buckling of the two legs soon established. Flat post-tensioned slabs with a thickness of 22cm, extend directly between shear walls. This structural arrangement maximizes efficiency and creates a simple solution slab floor that can be built quickly. The flat slab scheme also provides flexibility in the distribution of the hotel room, adapts to the height from floor to floor and building flexibility in service delivery and coordination through each plant.
Height frames made with steel beams are within the mechanical floors level 23, connecting the legs of the tower and resisting high shear forces that occur when these are located above the central atrium. Downstairs, the post-tensioned plates resist horizontal thrust generated by the inclined legs.
Building design
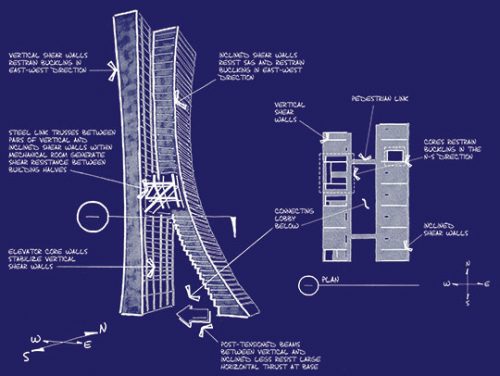
Due to the extreme tilt of the legs of the towers, walls opposed cutting and derive tend to flex laterally during construction. It was therefore crucial to carefully consider when designing the construction sequence, a simple structural analysis in place was not enough. To this end, Arup conducted a series of analyzes of the construction stages of the different scenarios of erection at the beginning of the design process in order to quantify the amount of displacement and locking the stress that builds up inside each tower in each scenario.
Additional studies showed that by introducing prestressing on the walls of vertical and inclined cut, movements and resulting tensions could be reduced further.
Measurements of the walls include:
- angular rotation on top of the tower
- Maximum lifting movement in all three axes
- differential movement between the vertical walls and sloping
- differential movement between adjacent bays walls
- differential movement between the three towers, which affects the support given to SkyPark
Moreover, the immediate displacement resulting from the effects of weight itself is offset by a pre-fall during construction. However, because of its asymmetry, further complicated by the concrete creep and shrinkage effects, are expected to continue their lateral deformation towers until these movements converge, after about 30 years.
SkyPark
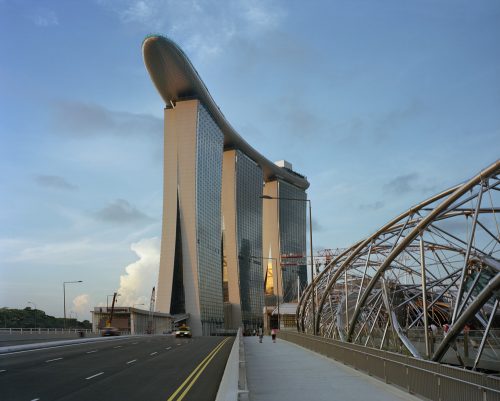
With its 340 meters long, 40 wide and an overhang of 64.92 meters, at a height of 198.11 meters above ground level, the hotel terrace SkyPark is the longest living and observation deck cantilevered world and has become a symbolic icon Singapore.
To succeed, the design had to reconcile several demands: the aim of creating an elegant aesthetic to the park above the towers, minimum weight and efficiency necessary to limit the adverse effects on the towers below demands, and constructability requirements necessary for the pre-assembly and rapid construction on the site.
- Structural optimization studies
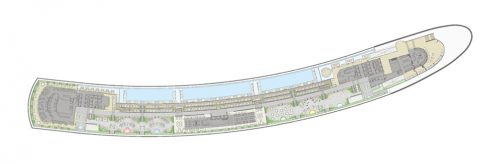
Several framing options were considered for the SkyPark at the beginning of the design process. These included various bars, beams, steel somiers, and alternative hollow concrete segmental bridges, among others. All these systems were evaluated for weight and ease of construction of both.
The design team, together with manufacturers and assemblers, converged on a system of post-tensioned segmental box girders with steel, 10 meters long and 3.60 meters wide, as the primary structural system for the segment cantilever, and a system of primary bridge with steel trusses for those segments that span between towers hotel. The bridges directly above each tower support struts steel rakes “V” extending from the roof of the hotel directly through the walls of reinforced concrete. The segments between each section of the tower beam simply supported at the ends of adjacent segments.
The relative displacements of the three towers vary dramatically, due to subtle geometric differences. Movement joints located between each tower accommodate such differential movement resulting from thermal expansion, wind-induced motions, and other time-dependent lateral movements generated from creep and shrinkage resulting from the asymmetry of the towers. Minute details through infinity pool accommodate these joints giving the impression of a clear and continuous monolithic deck through the towers.
Another important design consideration Skypark cantilever was his response to wind induced vibration, and vibration arising from the rhythmic human activity like dancing or running. Introducing a tuned mass damper 5 tons cantilever design serves to mitigate these effects. Subsequent dynamic tests of Skypark have verified the success of this system.
The primary segments 14 of the platform were prefabricated off-site, each section of the bridges that extend between adjacent towers comprise three beams 400Tn bridge level pre-assembled. The final part of the cantilever was equally precast segments to ensure proper fit during assembly on site. In total more than 7.000tn structural steel were used to erect in 13 weeks this Airpark.