Gateway Arch
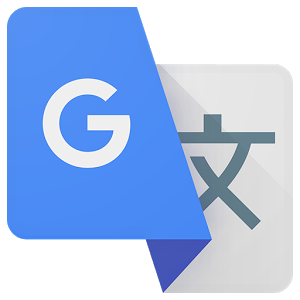
Introduction
After the Second World War, an event that stopped the development of the Memorial in honor of Thomas Jefferson, third president of the United States thought of an architectural competition to find the best design for a monument to symbolize the role of San Luis as gateway to the West.
a distinguished jury of architects, the director of the Museum of Philadelphia, the dean of architecture at MIT, Louis Labeaume and Charles Nagel Art Museum of St. Louis was established.
In the competition held between 1947-1948 for the design of the Jefferson National Expansion Memorial was winning Eero Saarinen, a Finnish-American architect who designed the Dulles Airport near Washington, DC, the General Motors Technical Center near Detroit the famous futuristic TWA terminal at the airport John F. Kennedy of New York, exceeding the 172 remaining projects, including his father Eliel Saarinen known and respected, with its design of an arc with 192m high.
Although most of the construction process took place a few hundred meters from the ground, there was not a single casualty. Not only was the project completed a stellar safety record, but also was completed on time and perhaps more importantly within budget. This was thanks to the coordination and cooperation of hundreds of workers.
Location
The old west bank of the Mississippi River, in St. Louis, United States, was selected in 1935 as the site to erect the monument. The city bought an area of about 60 hectares and all the buildings were demolished with the idea of developing the Jefferson National Expansion Memorial, whose main component would be the Gateway Arch. The outbreak of World War II, the construction of the Memorial stopped.
Demolition work and cleaning the area began on October 9, 1939 but the completion of the Memorial was not until the 60s.
The historic Eads Bridge, the first structure for tubular steel bridge, completed in 1874 creates the northern boundary of the Memorial. On the southern border is the bridge designed by Sverdrup and Parcel, the first in the US to use an orthotropic design.
Concept
The Gateway Arch is a memorial that refers to the westward expansion of the United States in the nineteenth century, but also served to create jobs in the ‘ 60s.
One of the reasons that the judges of the competition were in favor of the design of the great arch was because it was compatible with the historic Old Courthouse in St. Louis Riverfront, located across the two main streets to western arc. They noted that the design of Saarinen, “by its very form sympathizes with the dome of the Palace of Justice, ” which is aligned on an east-west arc.
The arch is the highest man – made monument in United States, 192m to the top and the second – highest monument in the world after Eiffel Tower.
The Gateway Arch, in relation to its surroundings borrows the concept of Eads Bridge using tubular steel and makes use of the new concept of stress analysis and structural design of Sverdrup and Parcel with the use of steel plates and beams.
Spaces
The Memorial includes, besides the Arc, an underground visitor center located directly below. In the center is the Museum of Westward Expansion, which tells the story of the opening to the West in the 1800s are also theaters with film screenings on the subject and on the construction of the arch.
Access
Access to the arch is made from the metro B. Hartzog, Jr. Visitor Center, located directly below. Visitors are transported from the lobby to the observation deck at the top of the arc by a passenger train, with capacity for 40 visitors, consisting of 8 capsules that can carry 5 people each. At a speed of 104 meters per hour, the trip takes 10 minutes round trip.
Platform
The observation deck with 19.81×2,13m, is closed with glass windows that allow views to the east and west. There is also a conventional elevator maintenance on each leg to the stairs 113.38my 1076 on each side with steps from the base to the top of the arch. The elevators and stairs are for emergency use and maintenance.
Structure
Faceted stainless steel faces of Arco extend 192m between the outer sides of its triangular legs at ground level and its top rises 192m. The structure takes the form of an inverted catenary curve.
With its 192m high arch shape is created by equilateral triangles of steel were stacked one on another, getting smaller as they neared the top. The construction allows triangles inside the arc gap remains which helped not only with the weight of the structure, but also allows a tram system installed therein.
Legs
Each leg is an equilateral triangle with sides of 16.46ma ground level, decreasing to 5.18m at the top. The legs have double walls steel 0.91cm apart at ground level and 0.18cm above 122m. To mark 91.5m space between the walls is filled with reinforced concrete. Beyond that point steel reinforcements are used.
To construct the legs of the triangular sections Arch double wall placed one upon another and were then welded inside and out. The sections ranged in height from 3.66m to 2.44m at the base for two trapezoidal sections. The complex engineering design and construction is completely hidden from view, no real structural skeleton. Their skins internal and external steel are joined to form a composite structure, which give strength and permanence.
All you can see is the bright stainless steel outer skin covering the inner skin of carbon steel, which combine to carry gravity loads and wind from ground level.
Foundations
Prestressed
Each tensioning rod cluster required careful positioning as to bow in two directions, both to adapt to the curvature of the arc as the cross section tapering. With the steel structure in place, we proceeded to concreting in boxes of about 1.52m each. The bars are post-tensioned after 3,4474e + 7 (pascal) concrete reaching force 2,7579e + 7 usually after 7 to 10 days.
Depth
The reinforced concrete foundations sink to 18.28m depth and extend 9.14m in the bedrock, strongly contributing to the structural strength of the arc. The Severud, Elstad, Krueger & Associates structural engineers report that under a wind load of 150 km / hr deviate bow on top 46cm only east-west. Their supports are oriented in a north-south line.
To prepare the site for the foundations of Arc, the visitor center and museum, 8,495 m3 of earth and rock were excavated. Alloy rods or tendons tensioned steel, 252 in each leg, 16m sink below the top of the base to anchor the structure to secure its base form. At ground level, only the two outer corners of each triangular base are prestressed by two groups of steel rods 63.
Assembly
In the workplace, cranes equipped with a spreader bar placed tubular sandwich panels vertically in a storage area specially constructed. Previously, the sides of the triangular sections were prefabricated in the plant and sent to the site as three sides of a triangle. The assemblies of these sections in the right place require extremely meticulous controls for placing and welding the corners, but any additional pre-assembly in the workshop it was impossible because the resulting sections would have been too large for shipment.
. Triangular sections for the highest positions in the arc had smaller dimensions and may be manufactured and sent as three pieces in the form of a dogleg, each with a short side and a long side, thus connections corner they could make in running workshops for field teams a simple and fast welding.
Triangular sections welds needed for mounting some deformation suffered by the contraction caused by the heat of soldering, but later is forced into position to weld the legs, causing a slight buckling of the stainless steel surface.
Indoor facilities, including prefabricated steel stairs, pathways for conveyor passenger train, the utility pipes and electrical wiring were placed on each leg of the arch, both from the lower entrance and from the top, depending the level of the construction phase.
Legs or columns
The way that the arch was built it was getting starting with the base of each side and then was forging its way up until the two sides could meet in the middle, at the highest point of the arc. Engineers had to be very precise in the placement of each base, apparently had a tolerance engineering less than 1 / 64th of an inch or two columns not be aligned properly.
Both columns arc acted as an independent cantilevers before completion and rose at the same time without scaffolding. The first triangular sections, to a height of 22m were handled with crawler cranes operating from the ground. Above this height of two drilling towers climbers, each weighing 100 tons, it was used to lift 3.66m tall the remaining sections of 50 tons.
Materials
Eero Saarinen, conceived the construction of stainless steel arch and consulted with engineer Fred Severud its viability from the point of view of structural engineering, demonstrating once again the need to combine the skills of more than one discipline in order create a project of this magnitude.
The arch is constructed of carbon steel and concrete for strength and covered with stainless steel skin below.
In a cross section, each leg of the arch is an equilateral triangle double wall with a gap of 12.19m wide at the base tapering to 4.57m at the top core. 142 sections of steel triangles necesitaro to complete the structure.
The inner skin is carbon steel A-7, of 0.38cm thick, except at the corners where they have increased thickness to provide greater rigidity. The outer surface is made from 900 tons of polished stainless steel panels 0.62cm thick, which vary in size from 1.83 x 5.49ma 1.83x165cm. The exterior and interior walls are made in the sections on the soles of the Pittsburgh-Des Moines Steel Company, steel manufacturers and assemblers arch.
From the top of the wall section composite crown arc, all direct compression loads are carried by the outer stainless steel skin and skin carbon steel inside. Vertical steel diaphragms, placed in the center each 0.60cm, connecting the two skins and serve as reinforcements to prevent buckling of the inner skin. Spaced steel angles midway between each diaphragm harden the outer skin. Attachments of carbon steel reinforcements to the outer skin were performed using spot welds.
All sections of the arch were sent by barge to St. Louis. Sandwich wall sections placed one against another facing the stainless steel sides and secured with steel bars welded to them. The uprights were carefully covered for transporting wood and neoprene.